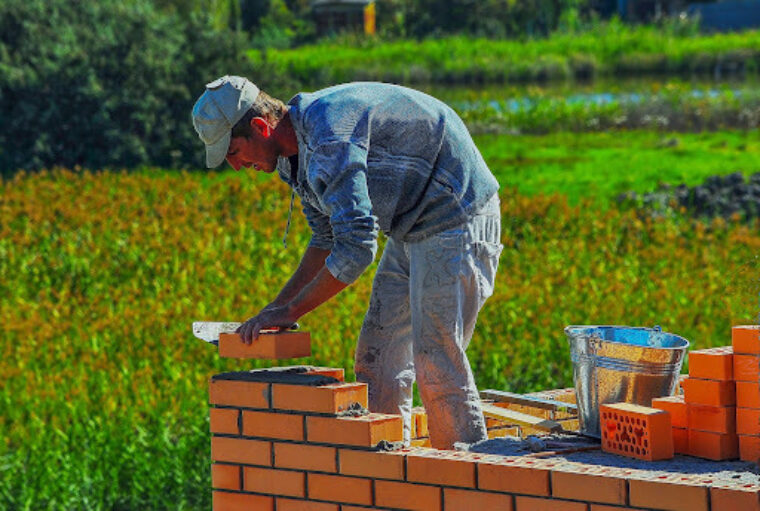
Before any interior finish work begins on a new construction project, the house or building must reach the point called “dried-in.” In some parts of the country, an inspector will check to ensure that no shortcuts have been taken in the process. Once the building passes the dry-in inspection, construction work can continue with the assurance that everything inside the building will stay dry.
What Does it Mean to Dry-In?
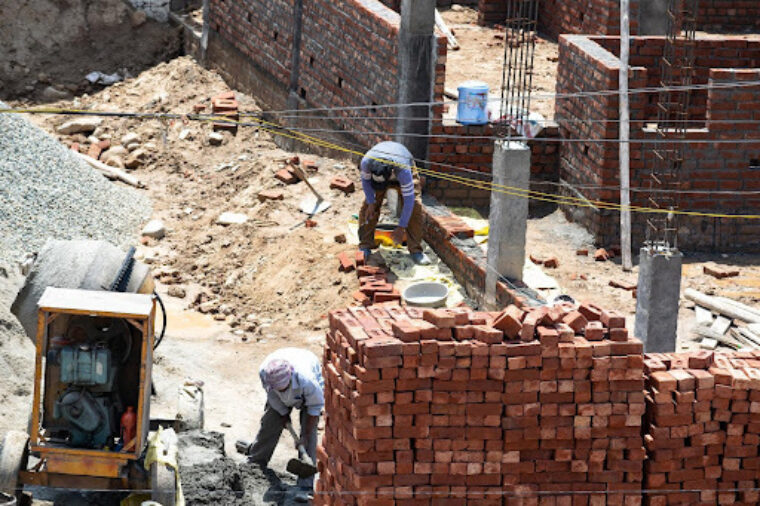
When a structure’s dry-in is completed, it can effectively keep the elements out to ensure that weather-sensitive materials aren’t damaged by rain, wind, snow, or other factors. This also helps decrease project delays due to inclement weather.
Why is it Important to Dry-In?
The term dry-in is significant in the construction industry because it establishes the point in the construction process where the rough exterior work has been completed: windows, doors, roofing felt or shingles and a weather-resistant barrier have all been installed. The contractor can turn their attention to the next stage in the process — roughing in the electrical, plumbing and mechanical components.
How Dry-In Protects Buildings
The term “dry-in” is used because it means the building is basically waterproof at this point. Finish materials can be stored inside the shell without fear of damage from the elements, and those working on the structure can complete their work under favorable conditions, taking their time to get the task done right the first time.
Once the building has been dried in, the contractor can take this opportunity to protect the foundation walls and slab from water damage by applying waterproofing products to the walls and floors. This is the best time to address this, as there is no need to protect finished walls and floors during their application.
What Does Dry-In Protect Against?
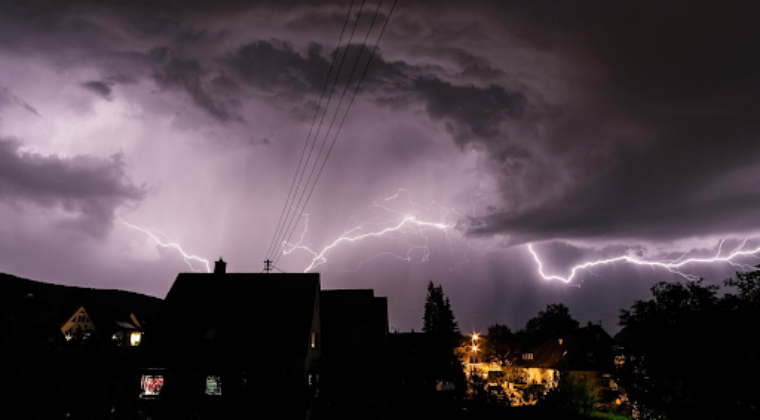
Before reaching dry-in, the building and everything inside it are subjected to all the elements of nature. Dry-in is the focus of preventing damage from these elements:
Wind
Wind can cause a lot of damage to a building during construction. It can blow away materials like shingles and roofing felt, and it can also cause water to leak into the building through window and door openings. A weather-resistant barrier, which is applied before dry-in, will protect the structure from wind-blown rain entering through the walls. This prevents moisture accumulation in the walls and the possibility of mold forming after the building is completed.
Rain
Rain can also cause serious damage to a building while it is under construction. Before the building is dried in, water can leak into the building through unprotected wall and roof sheathing and cause water damage, mold and mildew. Storing finish materials inside a building before the exterior envelope is secured is risky and could lead to lost time and money.
Snow
Snow can be even more dangerous than rain during construction. If it is allowed to accumulate on unprotected surfaces, it can rot the material it is sitting on while slowly dripping into the building over an extended period. Completing dry-in in areas subject to snow should be a top priority.
Use DRYLOK® for Superior Masonry Dry-In Products
DRYLOK manufactures several solutions to protect your building from water damage, and these can be applied during the dry-in process or after.
DRYLOK Original Masonry Waterproofer
This waterproofer is applied to any concrete or cinder block walls once the risk of water damage is past. Our original waterproofer protects against water leaks caused by winds up to 98 mph or ground pressure up to 10 psi. It is latex-based and lower in VOCs than solvent-based products. It takes two coats to warranty the waterproofing, and it can be applied with a roller or brush. It can be applied to masonry walls, bricks, stucco, concrete blocks and poured concrete.
DRYLOK Extreme Masonry Waterproofer
If your project is in an area prone to hurricane winds, our extreme waterproofer provides the protection of the Original Waterproofer, protects against winds up to 140 mph and is guaranteed to stop water with ground pressures up to 15 psi. DRYLOK Extreme can be applied to interior or exterior surfaces, as well as above or below grade. With just two coats, it provides a 15-year warranty. It is latex-based and can be cleaned up with soap and water. This product can also be tinted for a custom look.
DRYLOK Floor & Wall Masonry Waterproofer
Our non-pigmented masonry waterproofer is specially formulated for use on bare masonry floor and wall surfaces. It provides a durable, waterproof and easy to clean, non-yellowing high gloss finish that carries a seven-year warranty once two coats are applied. Easily applied with a brush, roller or sprayer, it provides protection to stop water with ground pressure up to 4 psi and winds up to 98 mph.
DRYLOK E1 Latex 1‑Part Epoxy Concrete Floor Paint
If your concrete floors are expected to receive heavy traffic or if you are protecting a garage, consider using DRYLOK E1 Latex floor paint. It provides a showroom-quality appearance with the protection of epoxy. It’s easy to apply and can be used on garage floors, basement floors, brick patios and poured concrete and block patios.
Rely on DRYLOK for Waterproof Protection
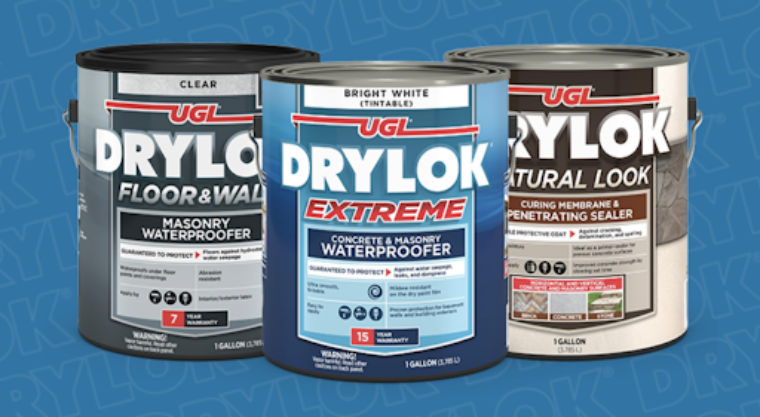
Whether you are a professional, DIYer or a homeowner looking for potential waterproofing solutions, our team and our products are here to help with your next project.
We carry other products that will seal your patios, pavers, bricks and much more. Consumers recognize DRYLOK as the number one name in waterproofing protection. Contact us today to find a retail outlet near you.